Comprehensive Overview: What is Porosity in Welding and Just How to stop It
Wiki Article
Understanding Porosity in Welding: Checking Out Reasons, Results, and Prevention Strategies
Porosity in welding is a relentless challenge that can significantly influence the quality and integrity of welds. As professionals in the welding market are well mindful, recognizing the reasons, effects, and avoidance techniques associated with porosity is vital for accomplishing robust and trusted welds. By delving right into the root triggers of porosity, analyzing its damaging impacts on weld quality, and discovering effective prevention methods, welders can improve their expertise and skills to create premium welds consistently. The detailed interaction of elements adding to porosity calls for a thorough understanding and a proactive strategy to guarantee effective welding outcomes.Typical Sources Of Porosity
Contamination, in the kind of dirt, grease, or rust on the welding surface area, produces gas pockets when warmed, leading to porosity in the weld. Incorrect shielding happens when the securing gas, frequently made use of in processes like MIG and TIG welding, is not able to completely safeguard the molten weld swimming pool from reacting with the surrounding air, resulting in gas entrapment and succeeding porosity. In addition, inadequate gas insurance coverage, often due to wrong circulation rates or nozzle positioning, can leave parts of the weld unsafe, permitting porosity to create.Impacts on Weld High Quality
The presence of porosity in a weld can considerably jeopardize the total high quality and stability of the bonded joint. Porosity within a weld produces voids or cavities that weaken the framework, making it a lot more vulnerable to breaking, corrosion, and mechanical failure. These gaps serve as anxiety concentrators, minimizing the load-bearing ability of the weld and raising the likelihood of early failure under used tension. In enhancement, porosity can also work as prospective sites for hydrogen entrapment, further worsening the degradation of the weld's mechanical residential properties.Additionally, porosity can prevent the performance of non-destructive screening (NDT) techniques, making it challenging to discover various other issues or gaps within the weld. This can cause considerable security problems, particularly in essential applications where the structural honesty of the bonded parts is paramount.

Avoidance Techniques Overview
Offered the harmful influence of porosity on weld high quality, reliable avoidance techniques are important to maintaining the structural stability of welded joints. In addition, choosing the suitable welding parameters, such as voltage, present, and travel speed, can assist minimize the danger of porosity development. By integrating these avoidance techniques right into welding practices, the event of porosity can be dramatically reduced, leading to stronger and extra reliable bonded joints.Value of Appropriate Protecting
Appropriate shielding in welding plays websites a crucial duty in protecting against climatic contamination and ensuring the stability of bonded joints. Shielding gases, such as argon, helium, or a blend of both, are commonly used to secure the weld pool from responding with elements airborne like oxygen and nitrogen. When these reactive elements enter into contact with the warm weld pool, they can create porosity, causing weak welds with minimized mechanical properties.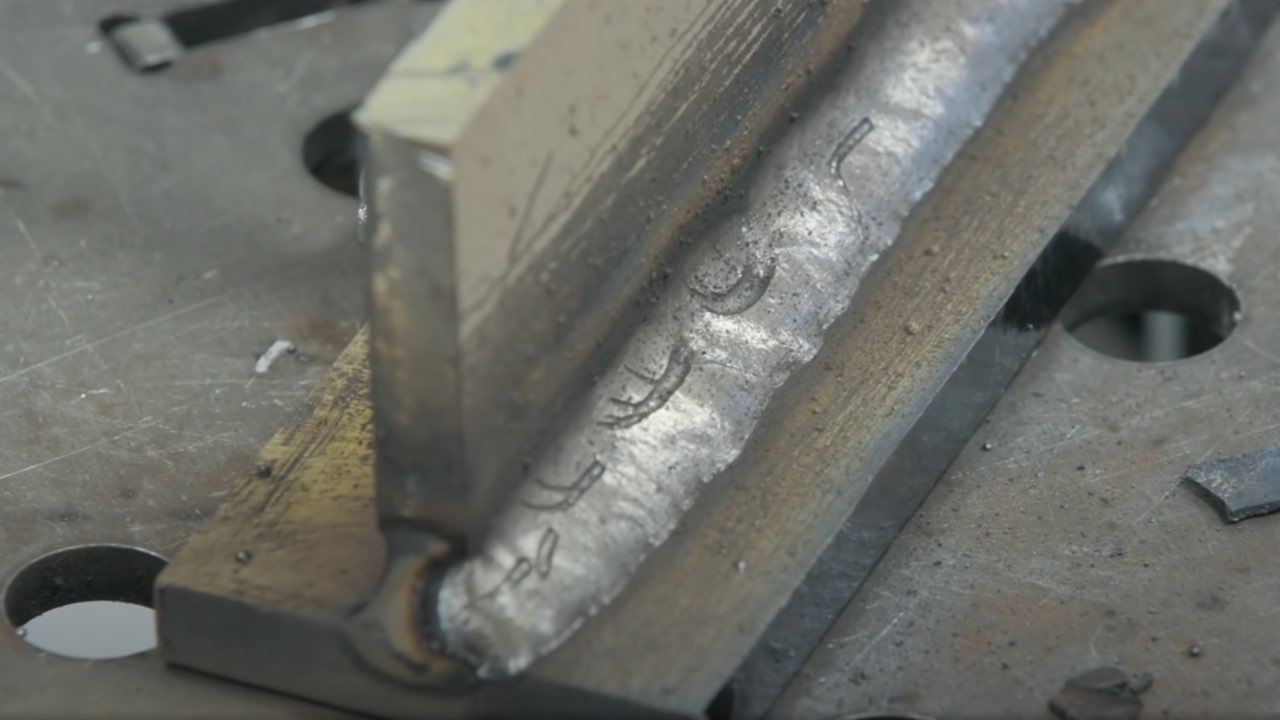
Poor shielding can lead to numerous problems official site like porosity, spatter, and oxidation, compromising the structural stability of the welded joint. Sticking to correct protecting techniques is vital to produce high-grade welds with minimal problems and make sure the long life and reliability of the welded elements.
Surveillance and Control Techniques
Just how can welders properly check and regulate the welding procedure to make sure ideal results and avoid issues like porosity? By constantly keeping an eye on these variables, welders can determine inconsistencies from the excellent conditions and make prompt adjustments to stop porosity development.
Furthermore, applying appropriate training programs for welders is essential for keeping an eye on and managing the welding process effectively. What is Porosity. Enlightening welders on the importance of keeping constant parameters, such as proper gas protecting and travel rate, can assist protect against porosity issues. Normal evaluations and accreditations can also make sure that welders are proficient in surveillance and managing welding procedures
Moreover, making use of automated welding systems can improve surveillance and control capabilities. These systems can precisely control welding specifications, lowering the likelihood of human error and making sure consistent weld quality. By incorporating innovative monitoring modern technologies, training programs, and automated systems, welders can efficiently check and control the welding procedure to minimize porosity problems and attain top notch welds.
Conclusion

Report this wiki page